With its revolutionary Plastic2Oil (P2O) technology, Plastic2Oil Inc. has pioneered the development of a process that derives ultra-clean, ultra-low sulphur fuel which does not require further refining, directly from unwashed, unsorted waste plastics.
Key Differentiators of Our Process
At Plastic2Oil, we advocate environmental sustainability while energizing local economies through the creation of green jobs. We expect our P2O technology will transform waste management practices to redefine the recycling landscape, how we recycle tomorrow and into the future.
Validation & Permitting
Reputable independent labs have validated the P2O technology including IsleChem (process engineering) and Conestoga-Rovers & Associates (emissions stack test). Plastic2Oil has been issued all necessary permits to operate by the New York State Department of Environmental Conservation (NYSDEC). Engineering report performed by SAIC validates and verifies the technology and economics.
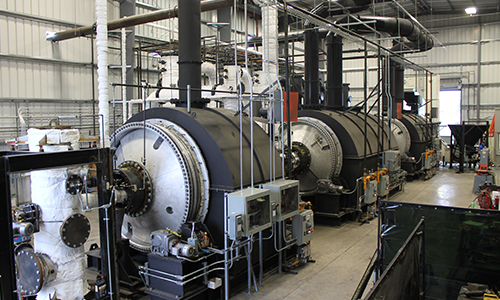
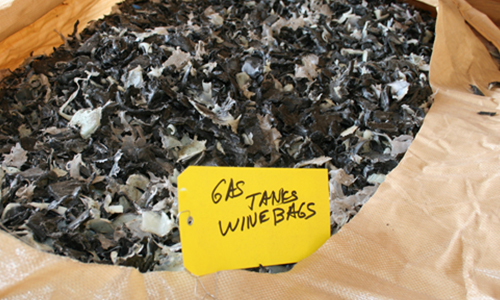
Processor
The processor requires only 4,500 sq. ft. of operating space. Height requirement is approximately 20 ft. Highly automated; very low operator to processor ratio. Modular design allows for easy deployment.
Inputs
The P2O processor accepts unwashed, unsorted waste plastics. Optimal feedstocks include polyethylene and polypropylene. The P2O process is permitted by the NYSDEC for up to 4,000 lbs. of plastic feedstock per machine per hour at the Company's Niagara Falls, NY facility.
Process
The conversion ratio for waste plastic into fuel averages 86%. Approximately 1 gallon of fuel is extracted from 8.3 lbs. of plastic. The processor uses its own off-gases as fuel (approximately 10-12% of process output); minimal energy is required to run the machine. Approximately 2-4% of the resulting product is Petcoke (Carbon Black), a high BTU fuel. Emissions are lower than a natural gas furnace of similar size, and the quality of the emissions improve with increased feed rates. Results from the final stack test performed by Conestoga-Rivers & Associates confirm that the processor emissions are well within the limits allowable under a NYSDEC air permit. The process operates at atmospheric pressure, and is not susceptible to pinhole leaks and/or other problems with other pressure and vacuum-based systems. The reusable catalyst is produced economically. The fuel produced is refined and separated without the high cost of a distillation tower.
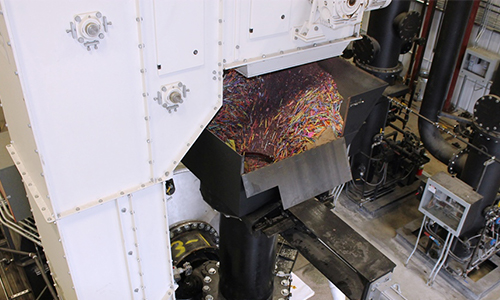
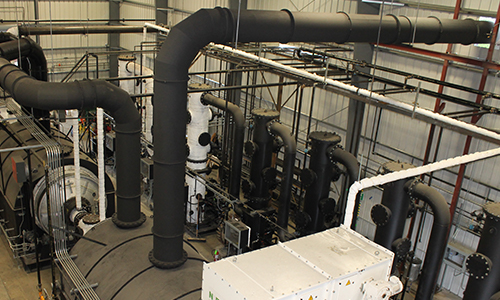
Resource Usage
The P2O processor is designed to use minimal amounts of external energy. As well as being beneficial for the environment, this is also a significant factor in the commercial viability of the process. Water is used for cooling only and usage is minimized through recycling the water in a non-contact closed loop. The water is not in contact with the process itself, keeping it clean and uncontaminated. Only 53 kWh electricity is required to run the fans, pumps and small motors. No electricity is used in the transformation of the plastic to fuel. Natural gas is only used on start-up to heat the reactor – once the processor is running, the reactor is heated with its own off-gases. A facility-wide gas compression system governs natural gas usage throughout the entire production process.
Fuel Output
Fuel quality has been validated by multiple independent petro-chemical labs including: Intertek, PetroLabs, Alberta Resource Council and Southwest Research Institute. All shipments leaving the P2O plant in Niagara Falls are tested by the Company's fully equipped internal fuel testing lab. Fuel is ready for sale upon completion of processing without the need for further refinement. From a single processor the Company can produce a range of fuel products, without further refining, including No. 2 Fuel (Diesel, Petroleum Distillate), No. 6 Fuel, Naphtha, Petcoke (Carbon Black), and Off-Gases to be used in the P2O process.
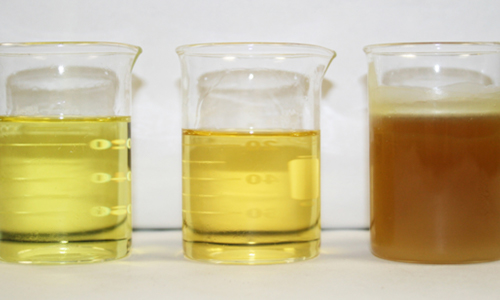